Engineering challenges in Bugatti Chiron’s production: The Bugatti Chiron stands as a pinnacle of automotive engineering, blending breathtaking speed, luxury, and cutting-edge technology. A true masterpiece of design, the Chiron is more than just a car—it’s a feat of engineering that pushes the limits of what’s possible in the automotive world. However, such extraordinary performance doesn’t come easy. The production of the Bugatti Chiron involves overcoming numerous engineering challenges, from materials selection to assembly, to ensure it meets the exacting standards of both speed and reliability. In this article, we will delve into the various engineering hurdles that Bugatti faced in bringing the Chiron from concept to reality.
Engineering Vision Behind the Bugatti Chiron

The Bugatti Chiron is designed to offer an unparalleled driving experience, combining extreme speed with unparalleled luxury. With a top speed of over 261 mph and a power output of 1,500 horsepower, the Chiron was conceived to be a hypercar like no other. The challenge for engineers was to ensure that the car’s performance didn’t come at the cost of safety or comfort, an intricate balancing act between technology, performance, and exclusive craftsmanship. The engineering vision behind the Chiron was not only to create a car capable of breaking speed records but also one that could maintain high performance on both the track and the road, offering a refined and comfortable experience for its elite clientele.
Design & Material Selection
At the heart of the engineering challenge was selecting the right materials that would contribute to the car’s performance without compromising structural integrity. Bugatti engineers had to use lightweight materials such as carbon fiber and titanium for the chassis and body panels, reducing weight while maintaining strength and safety. Carbon fiber, in particular, was crucial for achieving an optimal power-to-weight ratio.
The challenge in material selection also extended to the aerodynamics of the Chiron. The car’s sleek design features a custom bodywork tailored to achieve minimal drag while ensuring downforce at extreme speeds. The production of such specialized components, often requiring highly specialized molds and techniques, presented significant technical challenges in terms of both precision and cost.
Engine Development & Performance
The 8.0L quad-turbocharged W16 engine that powers the Chiron is a technological marvel in itself, capable of producing 1,500 horsepower. One of the biggest engineering challenges was ensuring the engine could perform at such extreme levels of power while remaining reliable and durable over time. The engineers had to design a turbocharging system capable of delivering near-instant acceleration without sacrificing performance or engine longevity.
Another obstacle was managing the immense heat generated by the engine. Cooling systems had to be designed with incredible precision to dissipate the heat efficiently while ensuring that the engine operated at peak performance. Additionally, turbochargers had to be precisely engineered to maintain optimal performance at such high speeds and power levels.
Transmission & Drivetrain
The seven-speed dual-clutch transmission engineered for the Chiron had to handle the car’s immense power without compromising acceleration or drivability. This transmission is one of the most sophisticated systems ever built, designed to offer seamless shifts at speeds where other cars would struggle. The drivetrain, which also integrates a four-wheel-drive system, was designed to ensure that the car could achieve unmatched traction and stability even at speeds exceeding 250 mph.
The challenge in developing the drivetrain was not just power distribution but also maintaining the car’s stability at such high speeds. Engineers worked tirelessly to create a system that could transmit the full force of the engine’s power to the wheels without sacrificing smoothness or reliability, both of which are critical for a car designed for extreme performance.
Suspension & Handling
One of the most difficult challenges faced by Bugatti engineers was designing a suspension system capable of handling the Chiron’s extraordinary performance while maintaining a comfortable ride for its occupants. Given that the Chiron was designed to be driven both on the road and at track speeds, the suspension system had to be incredibly adaptable.
The suspension was designed to ensure optimal stability and precise handling at high speeds, while also offering a level of comfort during regular driving. Achieving this delicate balance required advanced engineering solutions, including active shock absorbers and dynamic control systems that adjusted the suspension based on road conditions and driving speeds.
Manufacturing & Assembly
The manufacturing and assembly process for the Bugatti Chiron presents a unique set of challenges. The car is built in extremely limited numbers, with each unit requiring meticulous attention to detail. Every aspect of the Chiron is handcrafted, with artisans and engineers working in tandem to assemble the car’s complex components. Customization is also a key factor, as each car is tailored to the specific requirements of its owner.
With a focus on precision and quality control, Bugatti engineers work to ensure that every part of the car meets the highest standards. The challenge lies in maintaining the rigorous quality expected of a hypercar, even in a low-volume, high-cost production environment. Every component—from the hand-stitched leather upholstery to the high-tech electronics—must meet exacting specifications to ensure the car’s perfection.
Testing & Quality Assurance
Before a Bugatti Chiron reaches the road, it undergoes an intensive testing and quality assurance process. This includes testing the car’s performance under extreme conditions, such as high speeds and varying weather conditions, to ensure that it can handle the stresses of everyday driving and track-level performance.
Real-world testing of a car like the Chiron is a monumental challenge, given the complexity of its systems. Engineers conduct exhaustive tests to verify the car’s safety, reliability, and performance under both normal and extreme conditions. These tests are crucial in ensuring that the car not only delivers incredible performance but also offers peace of mind to its discerning owners.
Challenges in Meeting Regulatory Standards
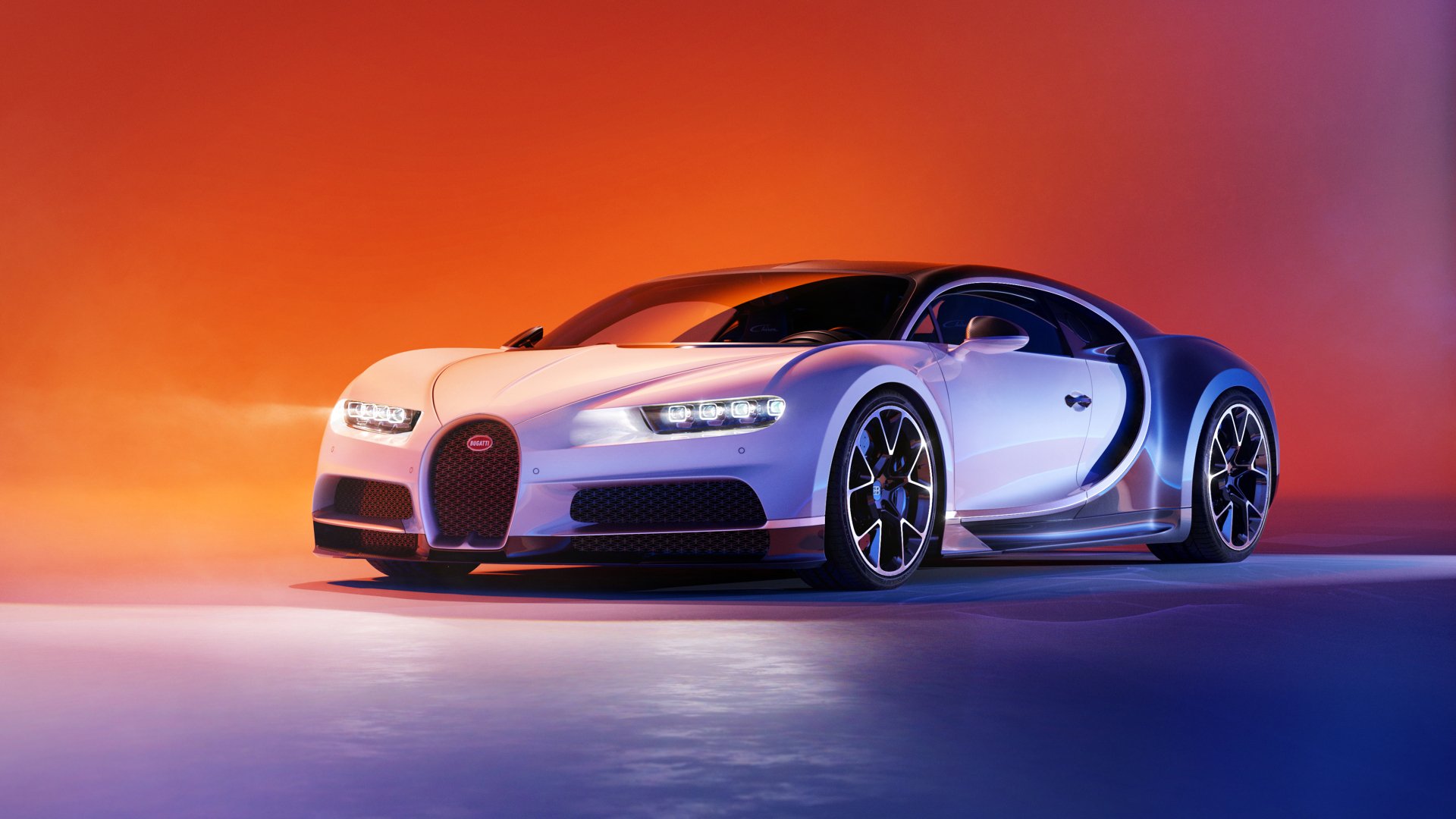
With hypercars being sold in global markets, meeting regulatory standards is an important and often complex aspect of production. The Chiron had to meet stringent safety regulations, emission standards, and noise requirements across multiple regions. The engineering team had to develop solutions to comply with these regulations without compromising the car’s performance.
This involved optimizing systems such as exhaust and emissions control, while maintaining the engine’s remarkable power and performance. Additionally, noise reduction had to be carefully engineered to meet global standards without compromising the sound quality that contributes to the car’s sensory experience.
Innovation and Future Engineering Challenges
The production of the Bugatti Chiron is not only a culmination of engineering excellence but also a glimpse into the future of hypercar development. Bugatti continues to innovate, with future iterations likely to push the boundaries of performance even further.
As electric and hybrid technologies advance, future Bugatti models will face new engineering challenges, such as designing battery systems capable of handling extreme performance demands without compromising weight or efficiency. Additionally, autonomous driving technology may also become a part of the Bugatti vision, presenting its own set of challenges in terms of integration with the car’s high-performance nature.
Conclusion
The engineering challenges in the production of the Bugatti Chiron are numerous and varied, reflecting the complex nature of building a hypercar that blends extreme performance with luxury, reliability, and cutting-edge technology. Every aspect, from materials selection to manufacturing and testing, requires an unparalleled level of precision and expertise. The result is a car that is not only a triumph of engineering but also a symbol of the potential for innovation and excellence in the automotive world. As we look to the future, the Chiron stands as a testament to the ability of engineering to redefine the boundaries of what’s possible in automotive design.
Tips for Understanding the Engineering Challenges in Bugatti Chiron’s Production
- Focus on Precision Engineering:
- The Bugatti Chiron represents a unique blend of speed, luxury, and precision. Every aspect of its production, from engine design to aerodynamics, demands incredibly fine-tuned engineering.
- Pay attention to how material selection (e.g., carbon fiber, titanium) is crucial for both performance and weight optimization. These decisions are not arbitrary but directly affect the car’s speed, safety, and handling.
- Understand the Importance of Customization:
- The Bugatti Chiron is highly customizable for each owner, which adds complexity to its production. From tailored interiors to bespoke aerodynamics, every Chiron is built to meet the specifications of its buyer.
- The engineering challenge is balancing customization with efficiency, while maintaining Bugatti’s high standards.
- Recognize the Role of Cutting-Edge Technology:
- The quad-turbocharged W16 engine and dual-clutch transmission are engineering marvels designed to produce extreme power and speed. Understanding these technologies will give you insight into the complexity of hypercar production.
- Active suspension systems, dynamic control, and real-time performance monitoring are all integral to the car’s handling and driving experience.
- Consider the Testing and Quality Assurance Process:
- Bugatti’s testing procedures are some of the most rigorous in the automotive world. Testing at extreme conditions—whether on the track or in real-world environments—is crucial to ensure reliability at high speeds.
- The focus on safety and performance testing is what sets Bugatti apart from regular sports cars.
- Research the Global Regulatory Challenges:
- Meeting global standards for safety, emissions, and noise is a significant part of the production process. Understanding how Bugatti engineers balance these requirements with high-performance goals can provide valuable insights into the complexity of hypercar production.
FAQs about Bugatti Chiron’s Engineering
1. What makes the Bugatti Chiron’s engine so special?
- The Chiron’s engine is an 8.0L quad-turbocharged W16, capable of producing 1,500 horsepower. The unique combination of four turbochargers ensures that the engine delivers consistent power without lag. This allows the Chiron to reach extraordinary speeds, while also maintaining smooth acceleration and responsiveness.
2. How does Bugatti ensure the Chiron’s stability at extreme speeds?
- The four-wheel-drive system and active suspension are key components that allow the Chiron to stay stable at speeds exceeding 250 mph. Additionally, the car’s aerodynamics are finely tuned to ensure downforce and minimize drag at high speeds, providing enhanced traction and control.
3. How does Bugatti balance luxury with performance in the Chiron?
- The Chiron is designed to offer not only extreme performance but also luxury and comfort. Handcrafted interiors, premium materials like leather and carbon fiber, and an advanced infotainment system ensure that every drive is a refined experience. The engineering challenge lies in creating a suspension system that can switch between comfort and performance depending on the driving conditions.
4. How does the Chiron’s dual-clutch transmission work?
- The Chiron features a seven-speed dual-clutch transmission that allows for extremely fast and smooth gear shifts. This transmission is designed to handle the immense power of the engine, ensuring that the car accelerates without interruption or loss of power. It is engineered to deliver seamless gear changes, which is crucial for a car designed for track-level performance.
5. What are the biggest challenges in producing a Bugatti Chiron?
- Some of the most significant challenges include:
- Material selection: Choosing lightweight but strong materials that do not compromise the car’s performance.
- Customization: Each Chiron is customized to meet the buyer’s specifications, adding complexity to the production process.
- Precision assembly: Ensuring that every component is built to exacting standards, given the low-volume, high-cost nature of production.
- Testing: Rigorous testing to ensure performance, reliability, and safety under extreme conditions.
6. How long does it take to produce a Bugatti Chiron?
- The production of a Bugatti Chiron is a highly intricate process that can take several months. Given the level of customization, meticulous attention to detail, and handcraftsmanship involved, production timelines can vary depending on the specific requirements of the car and its buyer.
7. What are the future engineering challenges for Bugatti?
- As the automotive industry evolves, future challenges for Bugatti may include integrating electric or hybrid powertrains into hypercars without compromising performance, maintaining sustainability in production, and incorporating autonomous driving technologies while ensuring they align with Bugatti’s performance ethos.
8. Why is Bugatti Chiron so expensive?
- The Bugatti Chiron’s price tag reflects the combination of cutting-edge engineering, exclusive materials, precision craftsmanship, and bespoke customization. The cost is also influenced by the extremely limited production, making each Chiron a rare and unique work of art.